Manage and Pay Contractors with Confidence
Remove the burden from your contractors to invoice you accurately.
Own and Optimize Your Budget with Real-Time Data Visibility
Manage and pay your service contractors what they have earned. With myTrack, you know costs are accurate and contract-compliant before payment.
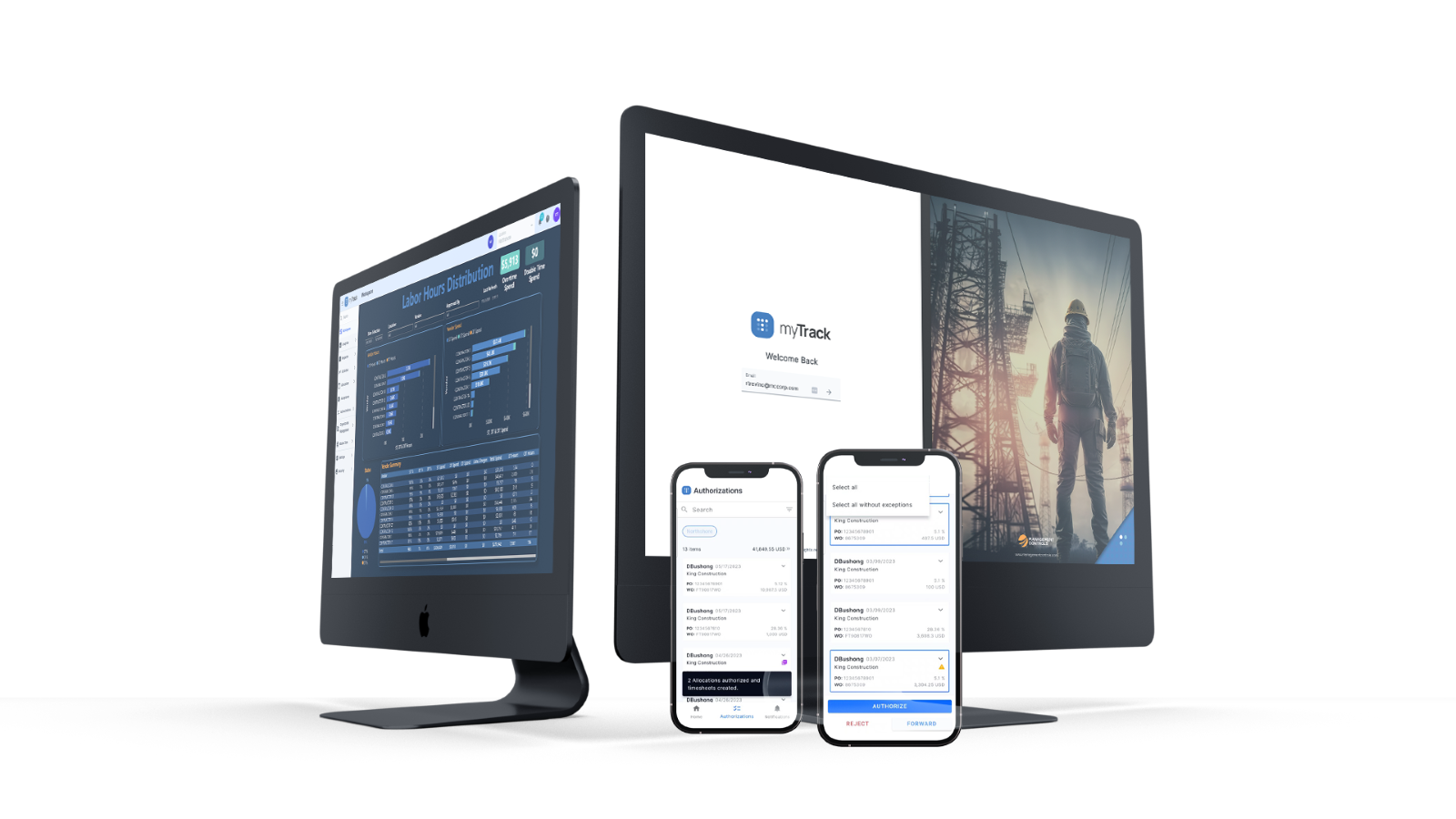
Data is Your Competitive Advantage
On a typical industrial site, contractor labor, equipment, and material costs are estimated, decisions are made in the dark,
and crucial data is spread across multiple systems. Sound familiar? With myTrack, you can measure, track, and
make informed decisions about your routine maintenance, shutdowns, turnarounds, outages, and capital projects in one place.
Gain real-time insights into your contractor relationships, ensuring compliance,
hour and dollar calculations, and seamless integration with your ERP system.
Contractors get paid accurately and on time, with labor and hours
validated through access control and gated systems.
Track Labor, Equipment, and Material Spend to the Penny
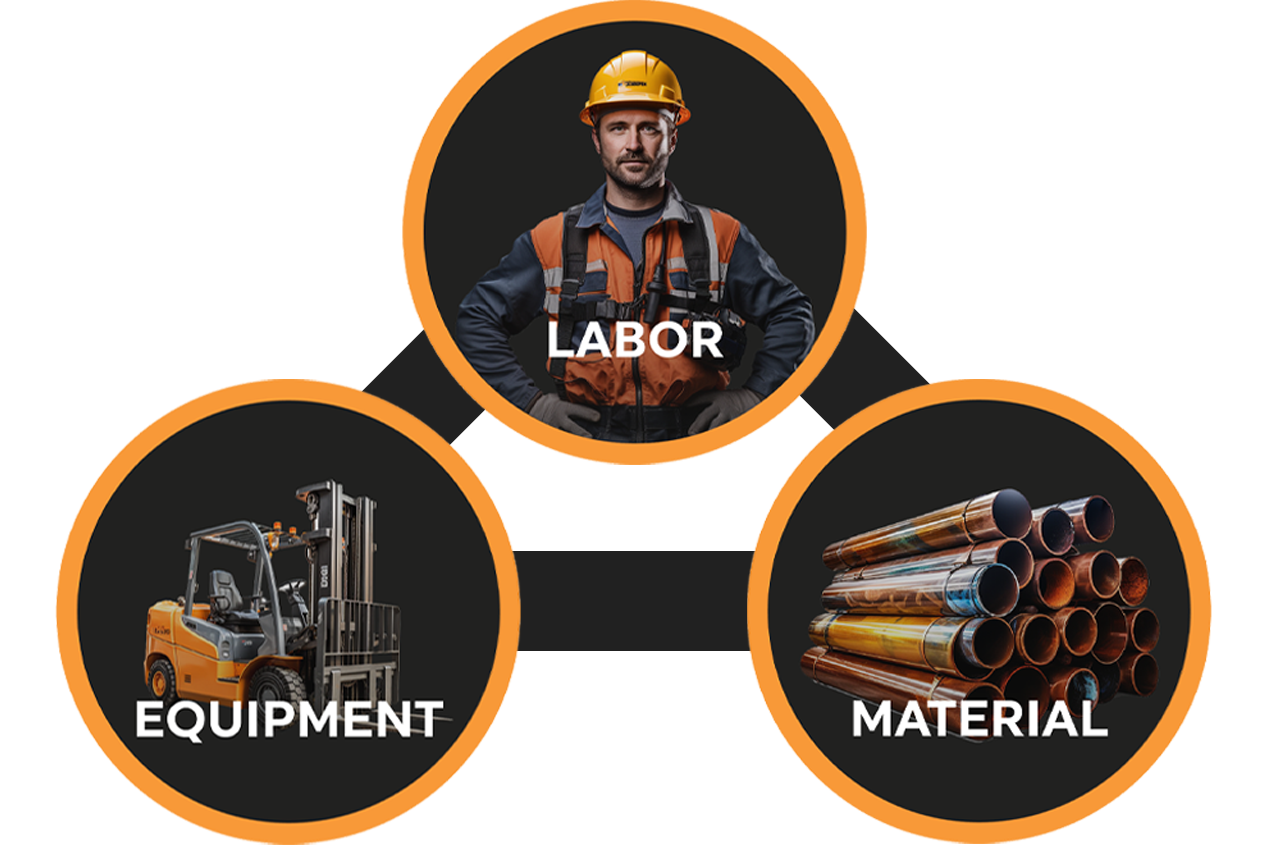
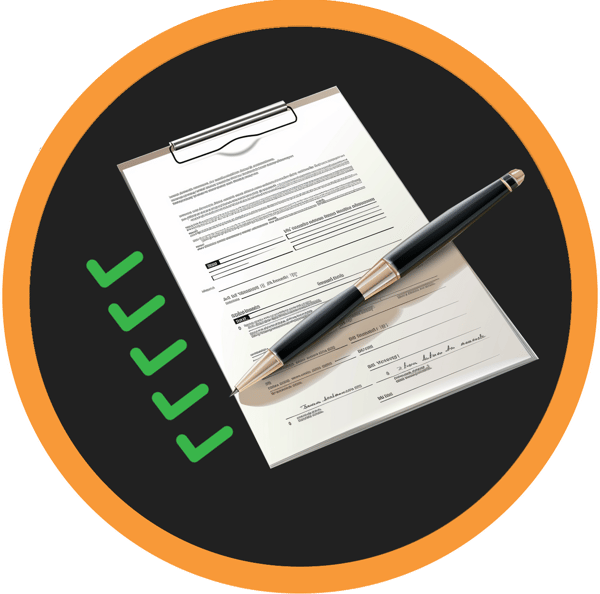
Automate and Simplify Contract Compliance
$
0
M
MATERIAL SPEND
TO DATE
Read what satisfied customers have to say ...
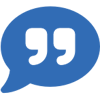
Without myTrack, you are operating in the dark. With myTrack, you actually know what your contractors have earned and you work with confidence that you are really paying for what you should be paying for.
— Vice President,
Maintenance and Manufacturing
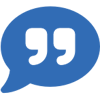
myTrack is quick and easy. What normally took me 10 minutes in Track now takes seconds.
— Vendor Timekeeper
Contractor Management Software
Lorem ipsum dolor sit amet, consectetur adipiscing elit
Lorem ipsum dolor sit amet, consectetur adipiscing elit. Mauris non sem auctor, lacinia sem non, egestas lorem. Maecenas at lobortis nisi, rhoncus rutrum leo. Sed vel tincidunt diam.
Keep Your Worksites Safe
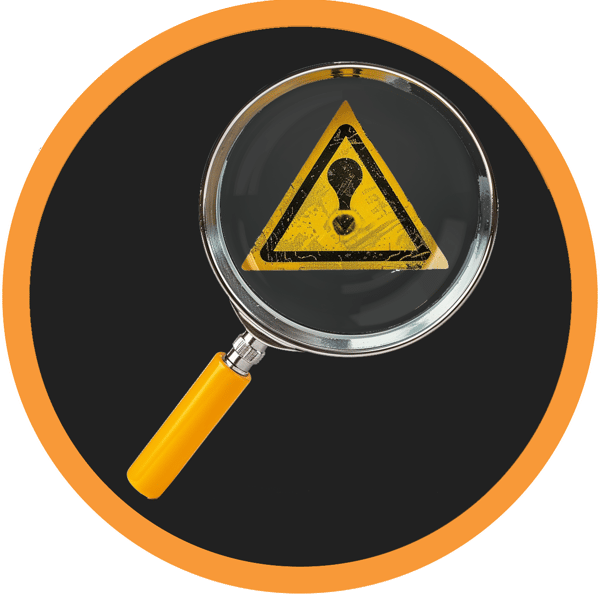
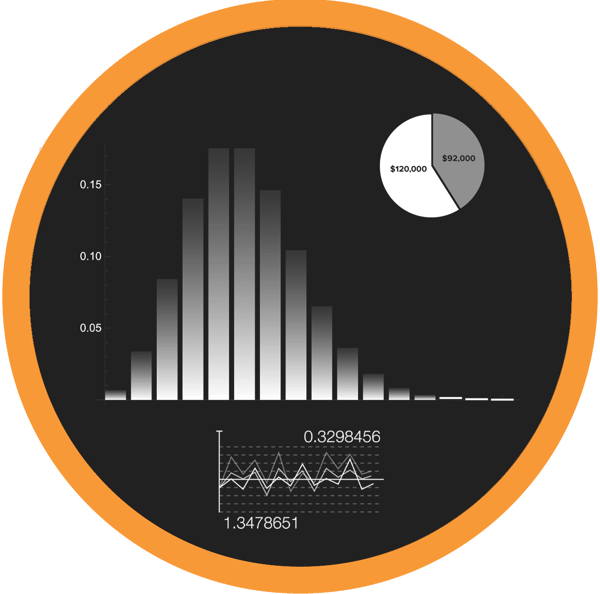
Make Better Decisions With Data and Insights
Why Choose myTrack?
.png?width=1635&height=1199&name=myTrack%20Mock%20Up%20Screens%20(1).png)
Be Proactive. Always Know Who is Onsite in Real Time
A better way to manage your global workforce.
Your Contractor Management Journey Begins with myTrack
$
0
M
MATERIAL SPEND
TO DATE
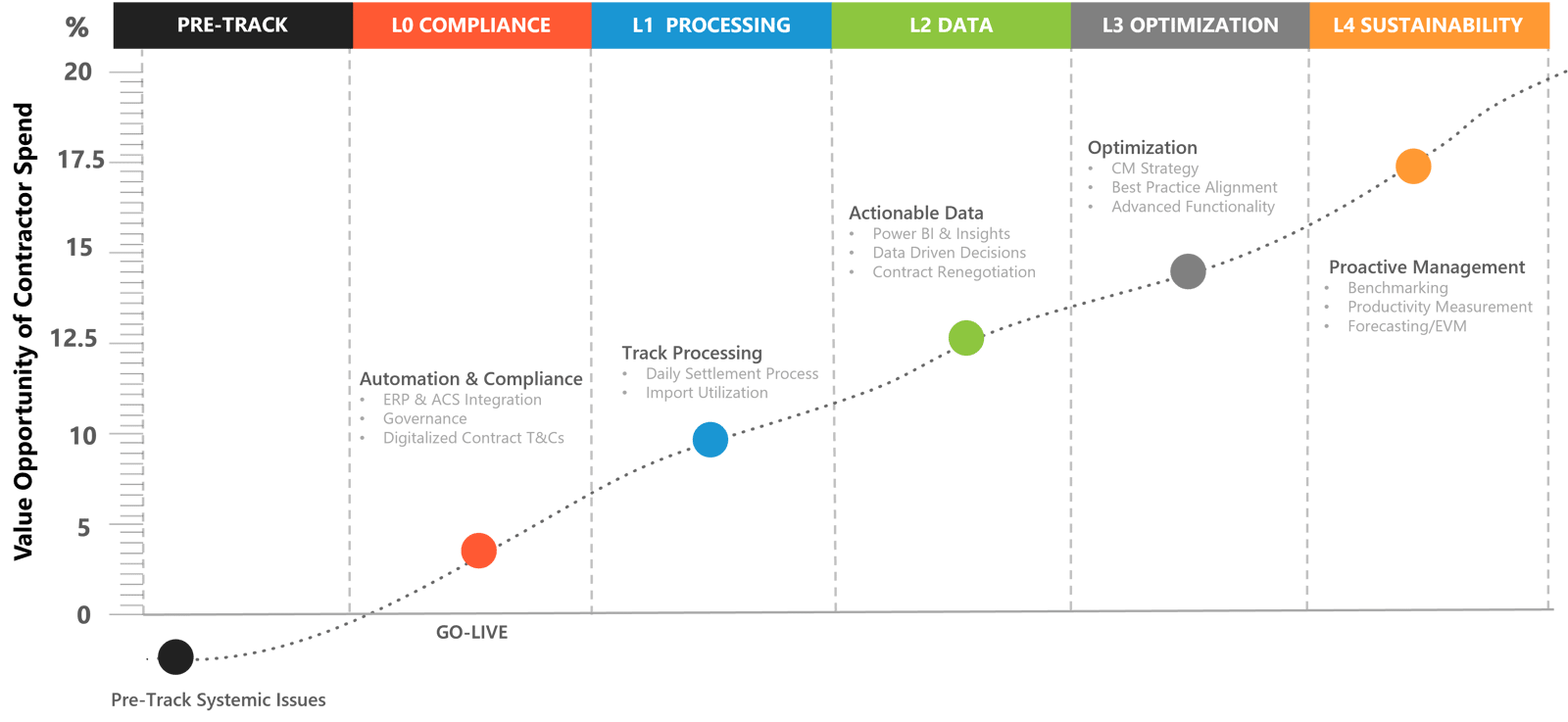
New myTrack Features
Personalized User Experience
myTrack’s modern look and feel means a more efficient, improved overall user experience--plus a faster daily settlement process with reduced clicks and quick access to data.
Personalized User Experience
Propel your business forward with software built on the cutting edge of technology. Our commitment to innovation means myTrack’s architecture is designed to grow with your business and emerging technologies such as AI, machine learning, and more.
Mobile Authorization
Improve productivity by authorizing hours and costs wherever you are with the myTrack mobile app. No more going back to the work trailer—spend more time in the field overseeing work.
Mobile Authorization
Propel your business forward with software built on the cutting edge of technology. Our commitment to innovation means myTrack’s architecture is designed to grow with your business and emerging technologies such as AI, machine learning, and more.
Built-in Intelligence
Leverage myTrack's intelligence for accelerated transactions, precise spend validation, visual alerts for data exceptions, and real-time notifications. Elevate your accuracy and efficiency in managing contractor data.
Built-in Intelligence
Propel your business forward with software built on the cutting edge of technology. Our commitment to innovation means myTrack’s architecture is designed to grow with your business and emerging technologies such as AI, machine learning, and more.
Open APIs
Cross-application spend controls are enabled through myTrack’s open architecture. Propel your operational efficiency to new heights with seamless integration with the other tools you rely on.
Open APIs
Propel your business forward with software built on the cutting edge of technology. Our commitment to innovation means myTrack’s architecture is designed to grow with your business and emerging technologies such as AI, machine learning, and more.
Reduced Administrative Time
Have one simplified workstream and a personalized experience. Get real-time alerts through in-app notifications and texts. Plus, it is easier to accelerate vendor onboarding onto myTrack.
Reduced Administrative Time
Propel your business forward with software built on the cutting edge of technology. Our commitment to innovation means myTrack’s architecture is designed to grow with your business and emerging technologies such as AI, machine learning, and more.
Robust Architecture
Propel your business forward with software built on the cutting edge of technology. Our commitment to innovation means myTrack’s architecture is designed to grow with your business and emerging technologies such as AI, machine learning, and more.
Robust Architecture
Propel your business forward with software built on the cutting edge of technology. Our commitment to innovation means myTrack’s architecture is designed to grow with your business and emerging technologies such as AI, machine learning, and more.
Settle with Your Contractors Daily with myTrack
Eliminate long settlement processes and reap the benefits of capturing real-time data.
2) ACS: Interfaces with client ACS to calculate instant workforce headcount and time-on-site or gross-time, or MCi’s Track Anywhere mobile application.
3) Terms, Conditions, Rates & Schedules: Applies contractor-specific terms, conditions, rates, and schedules (i.e. pay formulas) to gross time to calculate net billable hours.
4) Allocation & Acceptance [Daily Settlement]: Presents net billable hours for a contractor timekeeper to allocate each craftsman’s work for the prior day. Allocations include skill, billable rate(s), total cost, appropriate project cost objects, and responsible supervisor.
5) Authorization [Daily Settlement]: The owner’s supervisor approves or rejects accepted allocations designated for his or her approval. This person has access to all details of these allocations.
6) Visibility: Owners access data to analyze progress in the field, update schedules, and produce additional invoices if necessary; contractors utilize data for internal systems.
7) Completion: Authorized allocations are routed to the client’s ERP system as service entries (or other) and staged for payment to contractors.
